US +1800 764 0366 | Europe & Middle East +44 (0)115 980 3800 | Asia-Pacific: +61 2 7227 5369
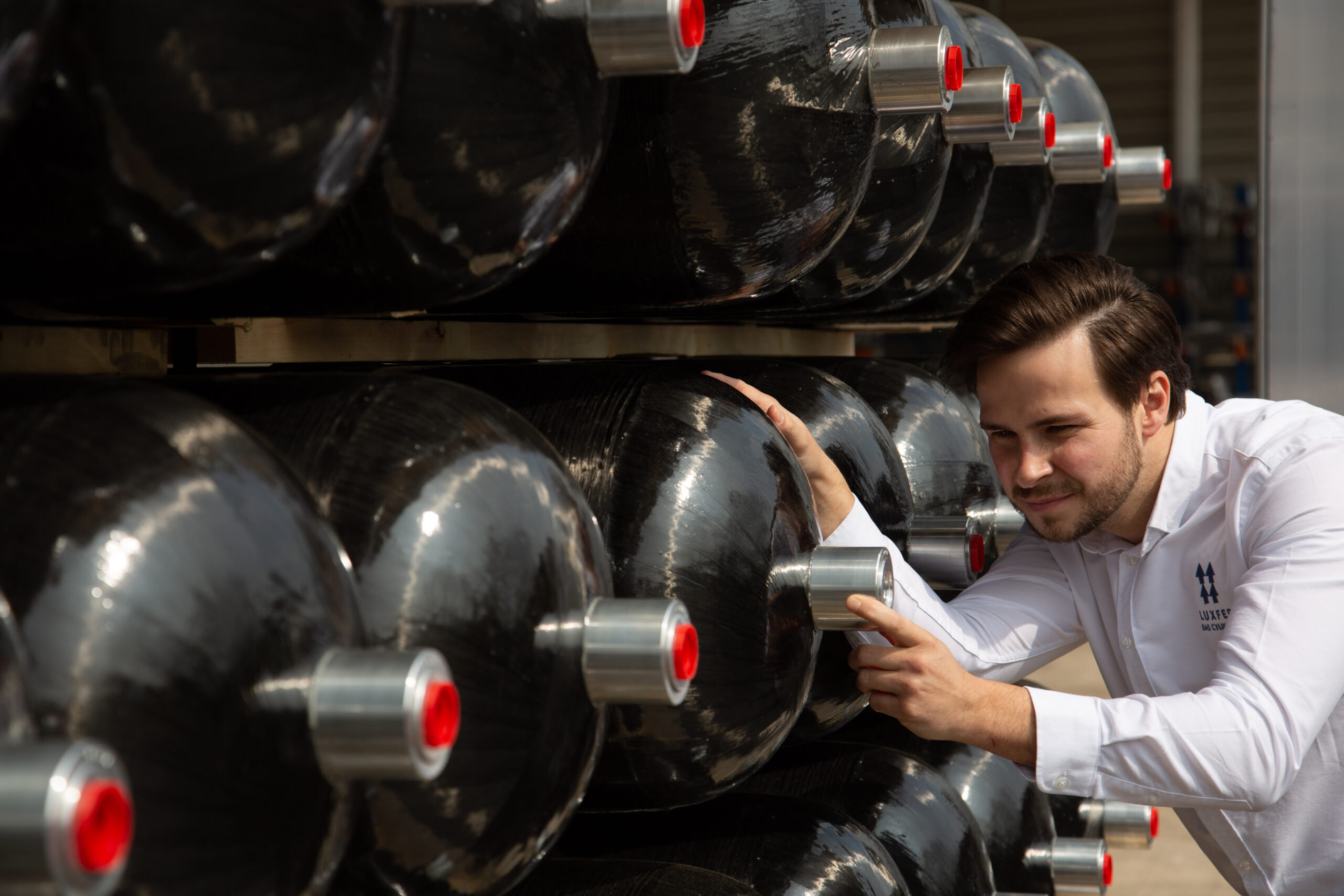
Support
Documents
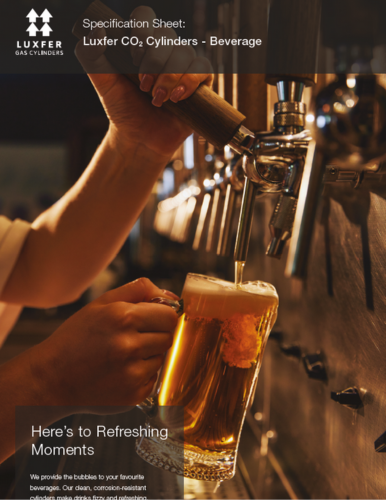
Luxfer CO2 Cylinders – Beverage

Luxfer G-Stor® Pro H2 Spec Sheet
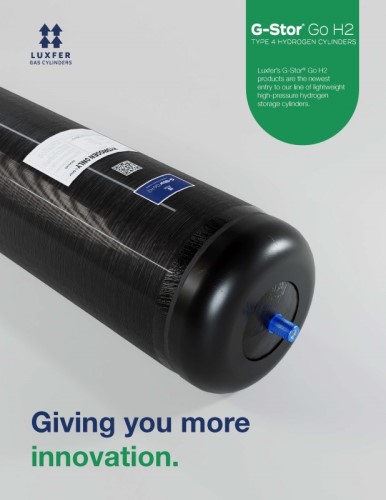
Luxfer G-Stor® Go H2 Spec Sheet
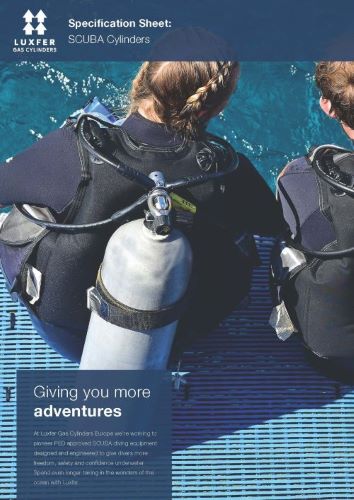
Luxfer SCUBA Spec Sheet
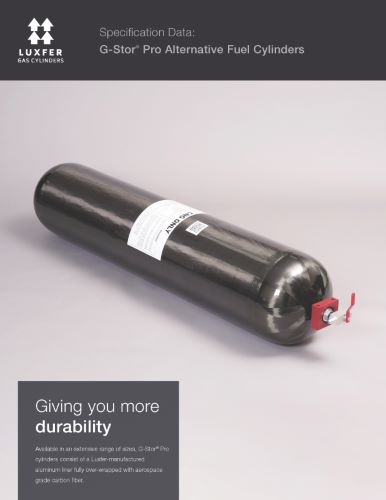
Luxfer G-Stor Pro Spec Sheet
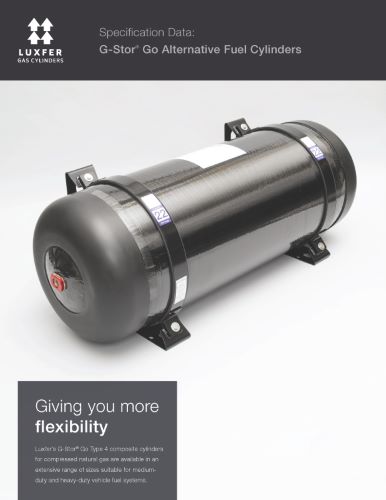
Luxfer G-Stor Go Spec Sheet
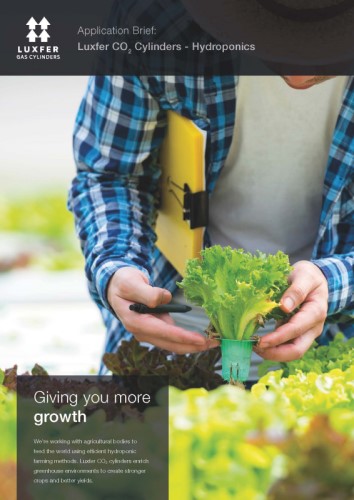
Luxfer CO2 Cylinders – Hydroponics
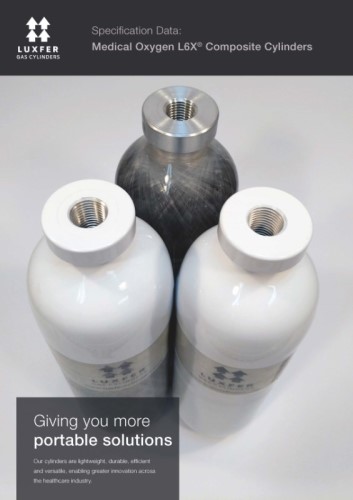
Medical Oxygen L6X Composite Spec Sheet
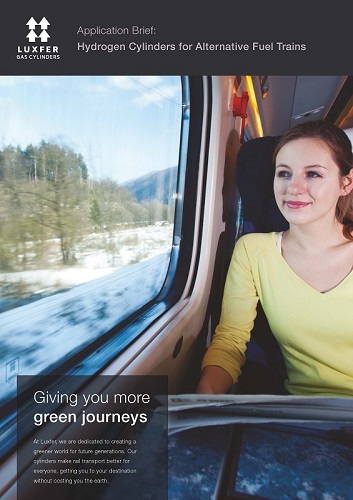
Hydrogen Cylinders for Alternative Fuel Trains
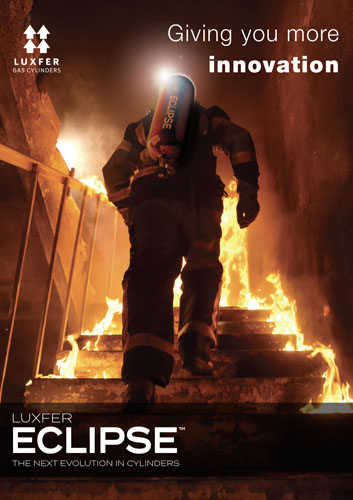
SCBA ECLIPSE brochure US 2019
Care & maintenance

Luxfer SCBA Delamination Repair Guide
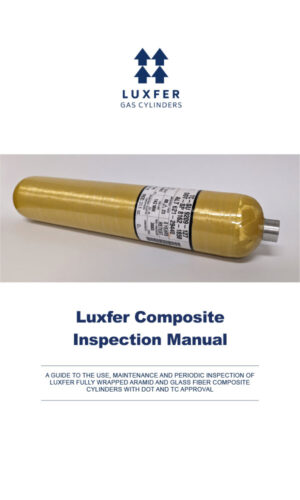
Luxfer SCBA Aramid-Glass Inspection Manual (DOT/TC)
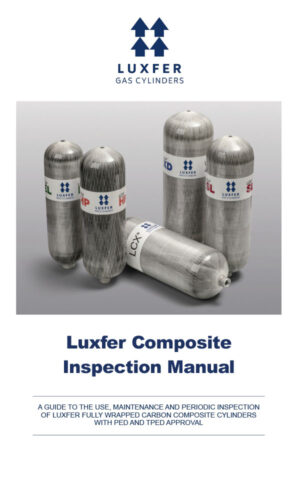
Luxfer SCBA Carbon Composite Inspection Manual (PED/TPED)
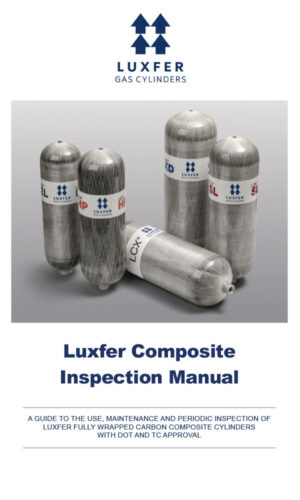
Luxfer SCBA Carbon Composite Inspection Manual (DOT/TC)
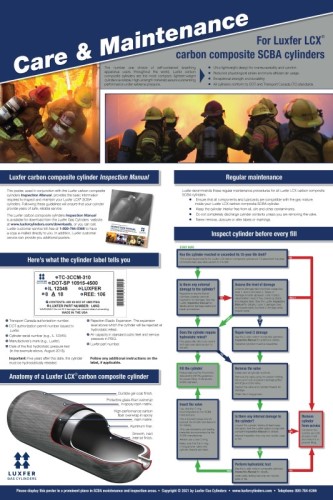
LCX care and maintenance poster
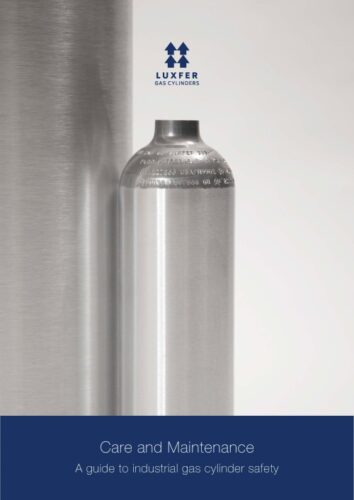
Industrial Gas Cylinder – Care and Maintenance
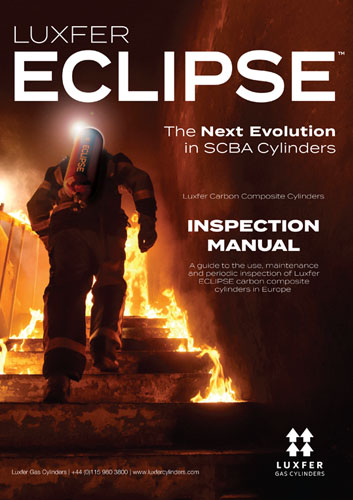
Luxfer ECLIPSE Inspection Manual
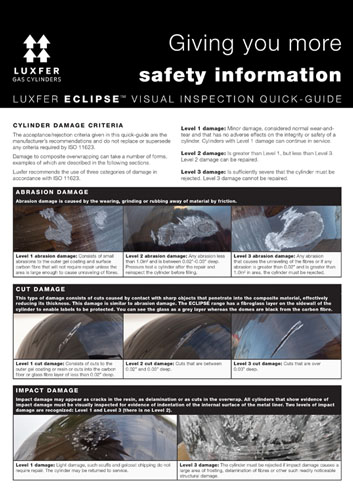
Luxfer ECLIPSE Visual Inspection Quick Guide
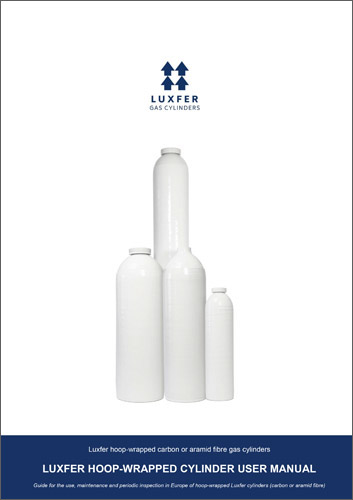
LUXFER HOOP-WRAPPED CYLINDER USER MANUAL
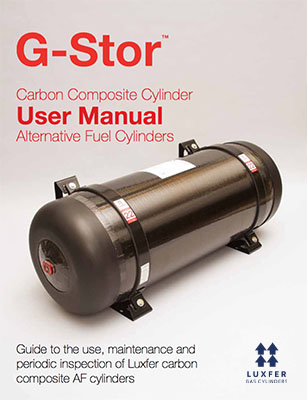
G-Stor™ carbon composite cylinder user manual Al
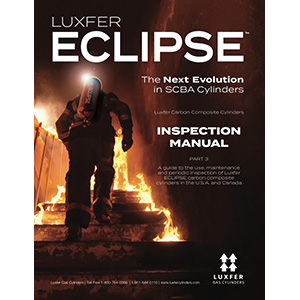
Luxfer ECLIPSE Manual
Resources & regulations
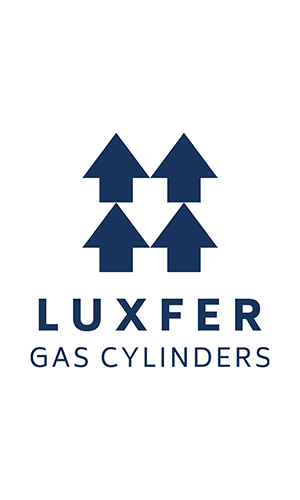
Transport Canada
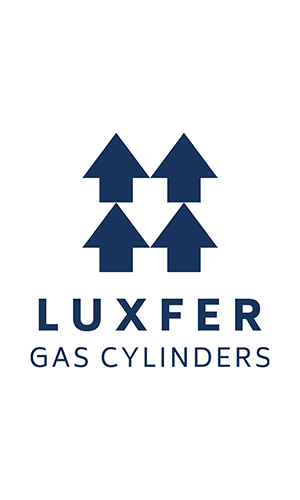
US Department of Transportation
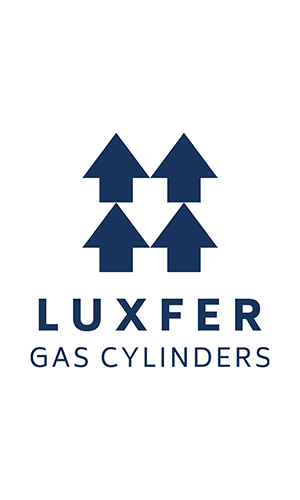
UK Health and Safety Executive
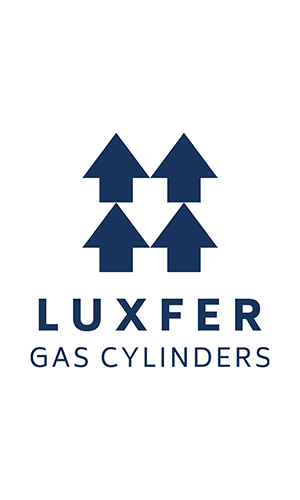
Appointed conformity assessment bodies – UK
Policies & certificates
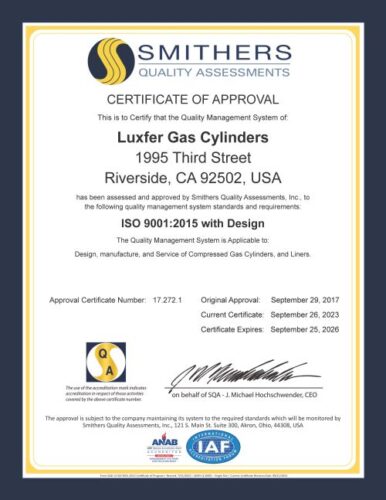
Luxfer Riverside ISO 9001:2015 Certificate
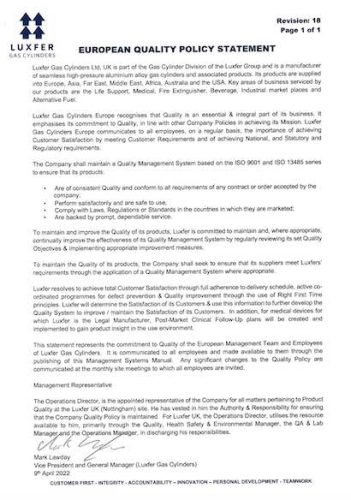
European quality policy statement
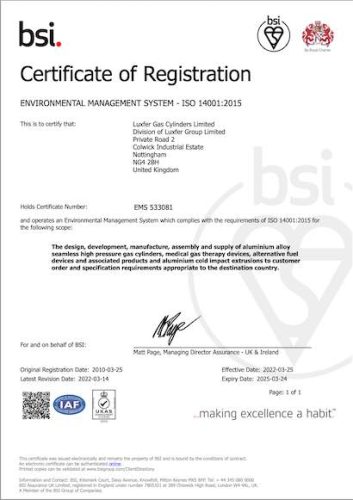
Luxfer Nottingham ISO 14001:2015 Certificate
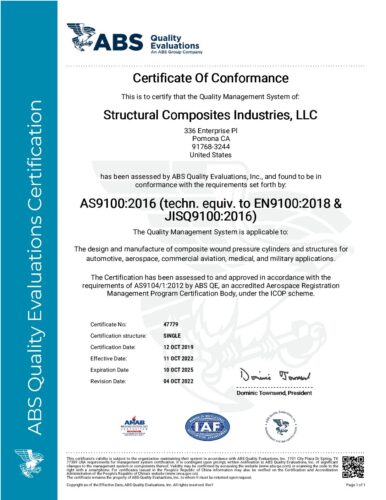
Structural Composites Industries AS9100D Cert
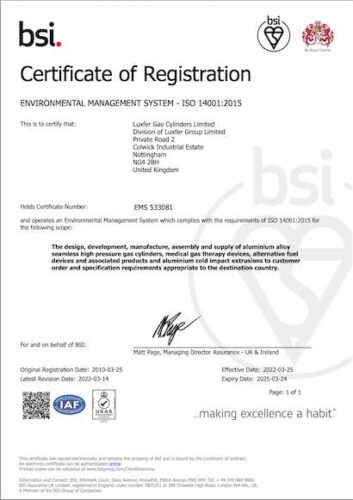
Luxfer Nottingham ISO 14001:2015 Certificate
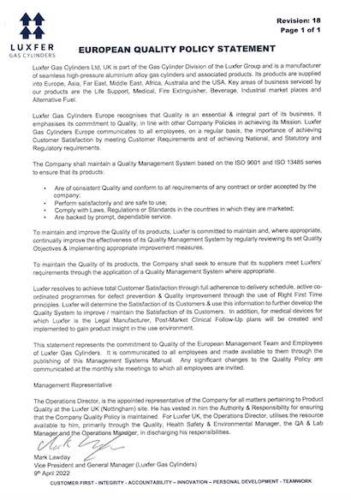
European quality policy statement
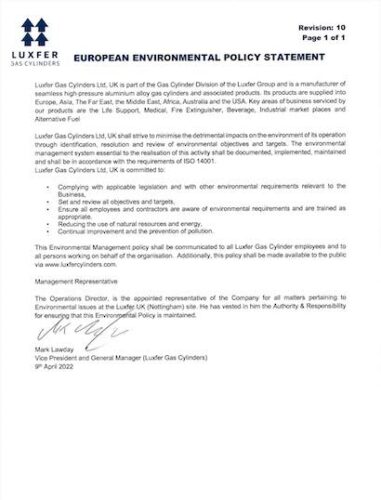
European environmental policy statement
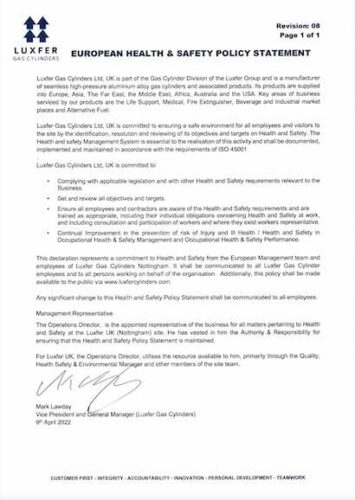
European health and safety policy statement
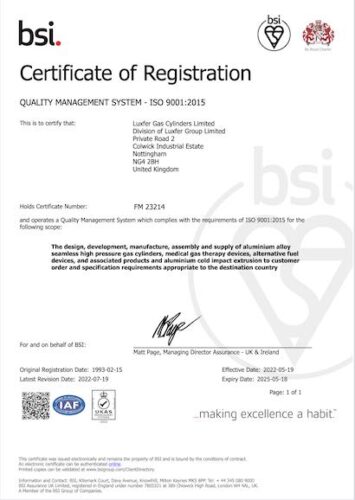
Luxfer Nottingham ISO 9001:2015 Certificate
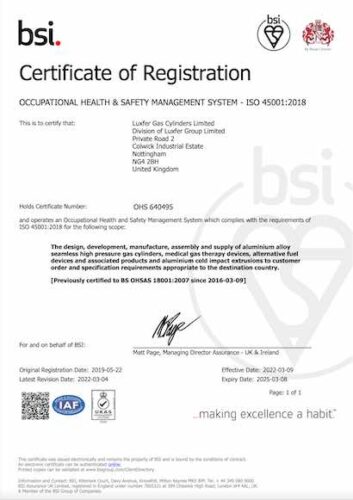
Luxfer Nottingham ISO 45001:2018 Certificate
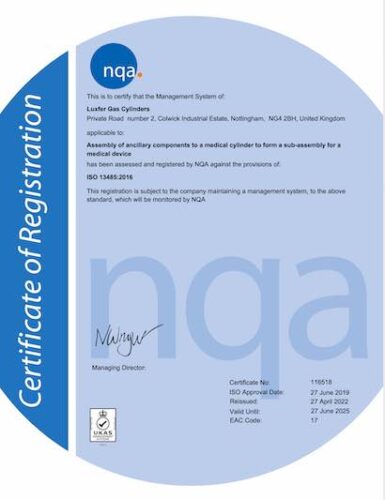
Luxfer Nottingham ISO 13485:2016 Certificate
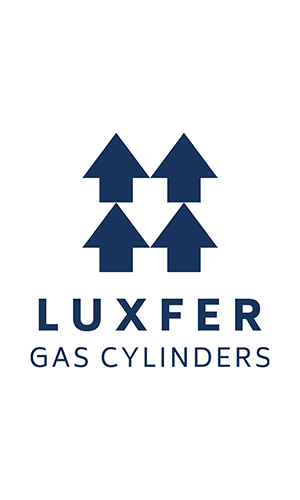
SCI Terms and Conditions
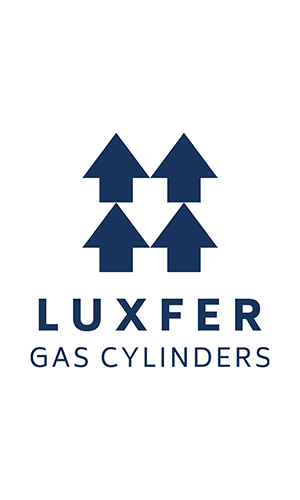
California Privacy Notice to Applicants
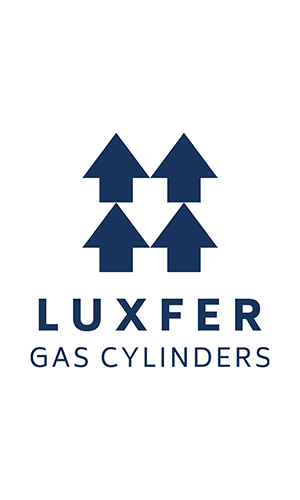
Modern Slavery Act 2015
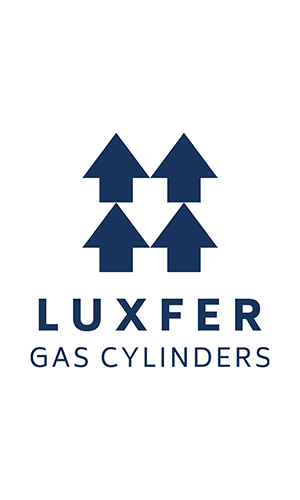
2018 Gender pay gap report
Technical bulletins
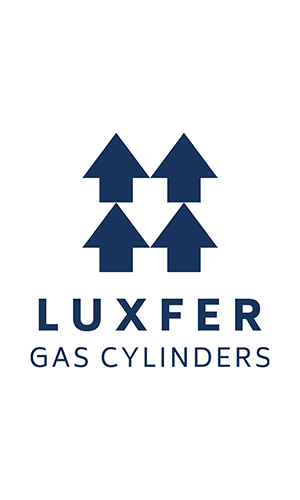
Luxfer position concerning composite cylinder delamination
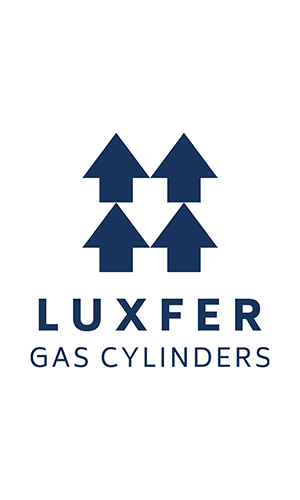
Luxfer does not require or recommend eddy-current
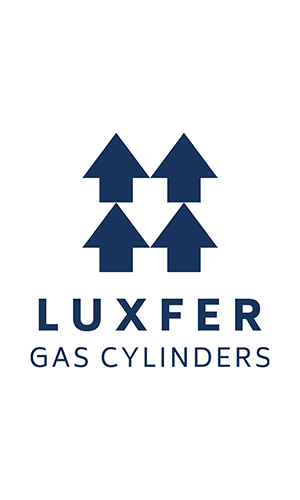
OTV Technical Bulletin
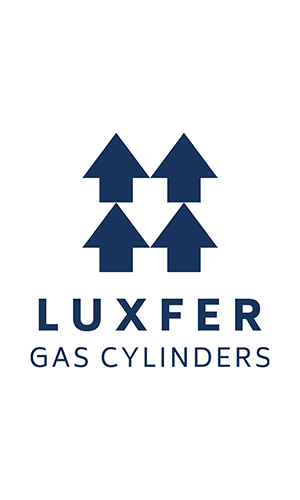
Statement for UK Diving Industry
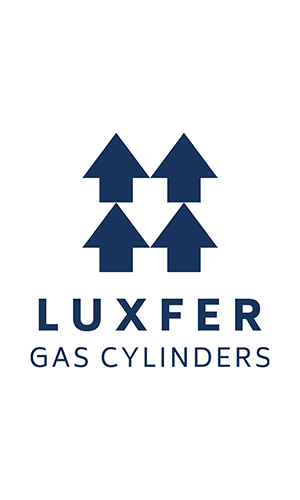
Recall notification
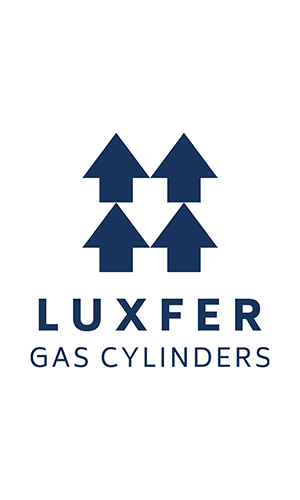
MRI compatibility of Luxfer aluminum and composite medical cylinders
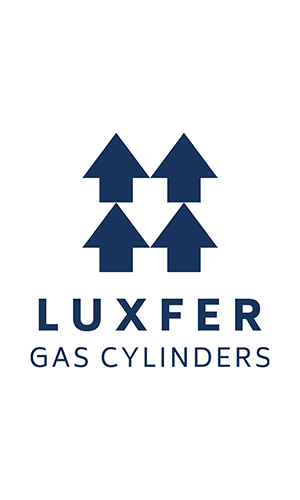
Luxfer position concerning life extension of DOT CFFC carbon composite cylinders
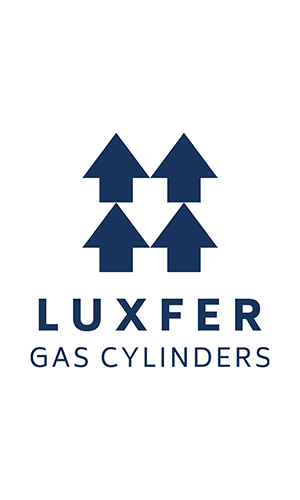
Sustained-load cracking (SLC) in ruptured scuba cylinder made from 6351 aluminum alloy
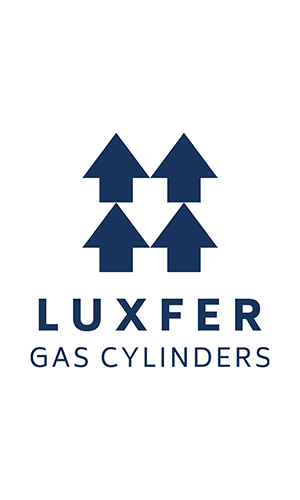
Paint removal and repainting of Luxfer all-metal and composite cylinders made from 6061 aluminum alloy (L6X®)
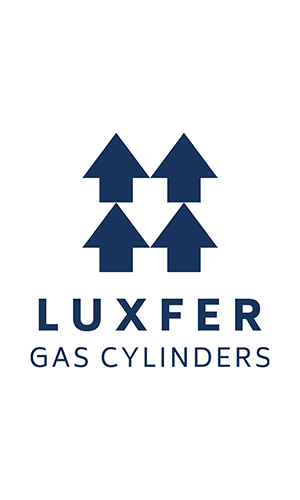
Luxfers Grundsatzerklärung hinsichtlich einer vorgeschlagenen längeren Nutzungsdauer von vollumwickelten Verbundflaschen
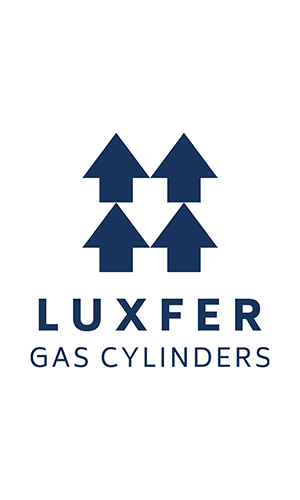
Politique de Luxfer pour l’extension de la durée de vie des bouteilles bobinées en composite
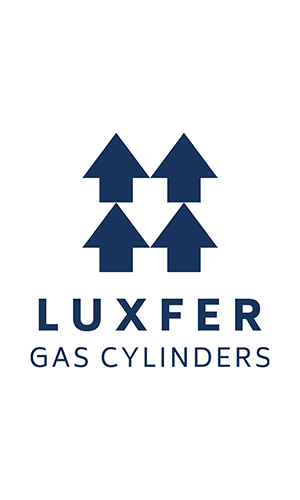
Luxfer clarifies difference between bowed and bulged aluminum cylinders
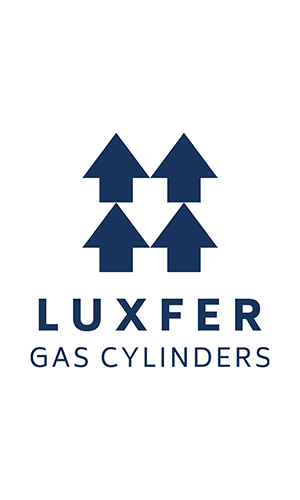
Dates when Luxfer changed its aluminum alloy from 6351 to 6061
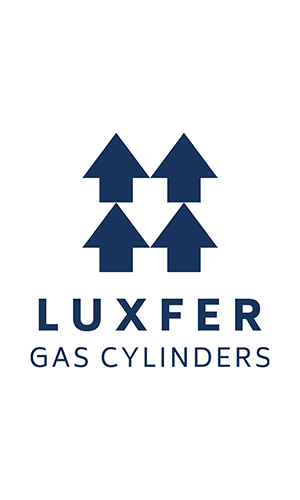
Dates of SCUBA cylinder aluminum alloy changes
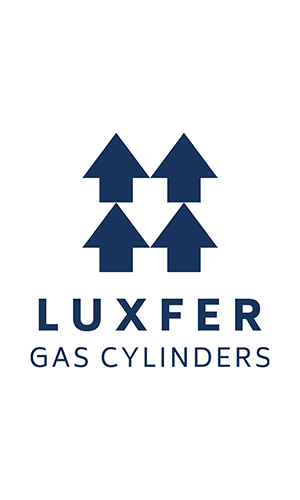
Temperature exposure
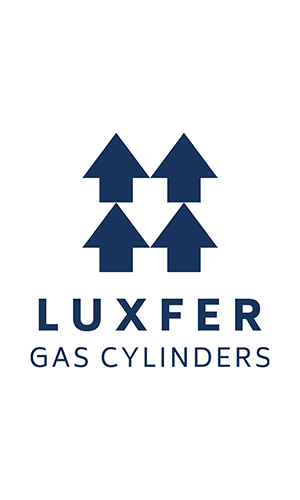
Paint strippers for aluminum cylinders
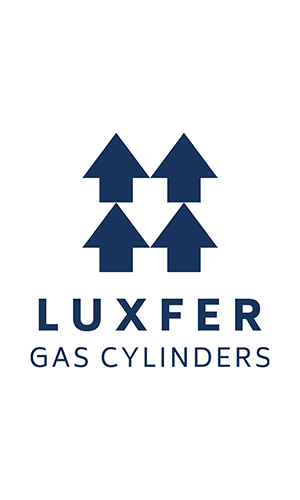
Cylinder OD cleaning procedure for brushed and unpainted cylinders
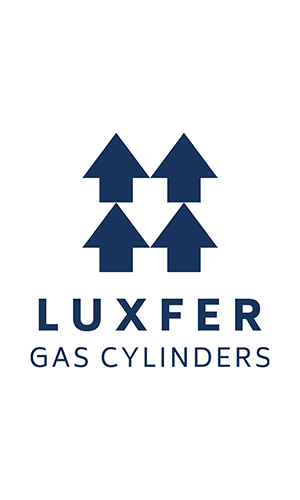
Cylinder ID cleaning procedure
Warranty information
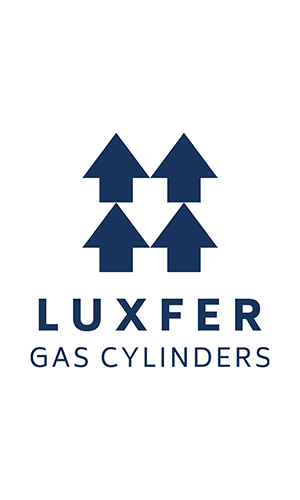
Warranty for cylinders manufactured in the United States
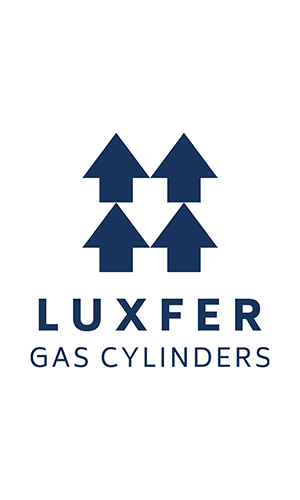
Limited warranty for Australia and New Zealand
Serial numbers explained
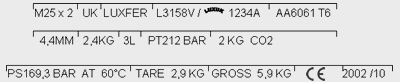
Typical markings for a CO2 fire extinguisher cylinder according to PED
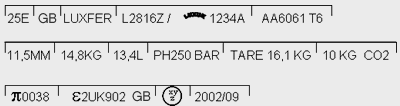
Typical markings for a liquefied gas cylinder according to TPED
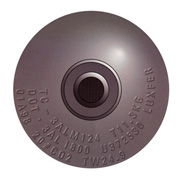
Aluminum cylinder serial numbers and markings
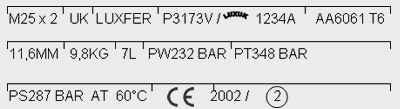
Typical markings for a SCUBA cylinder according to PED
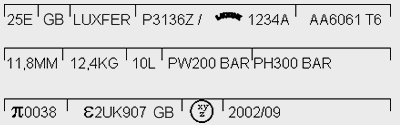
Typical markings for a permanent gas cylinder according to TPED
Did you know?
Luxfer was founded in Chicago, Illinois in 1897.
FAQs
Aluminum scuba cylinders in oxygen-enriched and oxygen service – I’d like to blend my own EAN mixtures. Is it all right for me to use Luxfer scuba cylinders for partial-pressure nitrox blending?
In all matters relating to gas-handling, blending and filling, Luxfer defers to CGA, of which Luxfer is a member. Partial-pressure blending with oxygen should be done only by those properly trained to do so safely by a recognized, responsible agency that strictly follows CGA guidelines. Most accidents related to partial-pressure blending have involved people who have not been properly trained.
Carbon composite cylinders for medical oxygen – will I need special handling equipment to protect the cylinder?
Luxfer’s carbon composite cylinders do not need any special handling equipment—in fact, they are the strongest, most durable cylinders ever made. Around the world, carbon composite cylinders are used daily in one of the most demanding, abusive environments imaginable—providing breathing air for firefighters while they battle blazing infernos. You’ll find care and maintenance for Luxfer carbon composite cylinders neither time-consuming nor expensive. For more information, call Luxfer toll-free at 800-764-0366.
Carbon composite cylinders for medical oxygen – what types of valves and regulators does a Luxfer carbon composite cylinder require?
Luxfer’s medical composite cylinders take standard valves and regulators. Please note that the 3,000-psi service pressure rating will require the valve to have the appropriate pressure release device, which is already available as a standard product from valve manufacturers. Luxfer will ensure that you get the proper valve with your cylinder when you place your order.
Carbon composite cylinders for medical oxygen – how do Luxfer carbon composite cylinders compare with liquid oxygen (LOX) systems?
Luxfer carbon composite cylinders are a profitable, cost-effective alternative to more expensive LOX systems because Luxfer composite cylinders allow you to leverage your existing filling and delivery equipment. Unlike LOX, composite cylinders do not require major investments in equipment and infrastructure. Moreover, since carbon composite cylinders cost less initially than LOX systems, you will recoup your initial investment and start getting your payback in far less time.
Carbon composite cylinders also offer significant advantages to oxygen users compared to LOX systems:
- LOX systems constantly vent whether being used or not. Carbon composite cylinders do not vent, and their contents can be stored until needed.
- Although some LOX systems are safer than others, hazardous liquid oxygen spills are always a possibility. Some units cannot be tilted 90 degrees or more without spilling-which can cause severe skin burns and increase the risk of dangerous oxygen-fed fires. Also, LOX transfilling can be difficult-especially for users with reduced hand dexterity-and potentially hazardous because of possible skin burns from touching liquid oxygen residue on connections. No such dangers exist with carbon composite cylinders.
- LOX requires expensive storage and delivery equipment, and because of special handling requirements, each home visit involving LOX is more time-consuming than visits to drop off and pick up cylinders. Carbon composite cylinders require no additional investment and allow you to use your current filling and delivery equipment.
- Some LOX portable units operate only with conserving devices, making them unsuitable for patients who require continuous oxygen flow. Carbon composite cylinders can be used with or without conserving devices, offering a continuous flow option for users who need it.
- LOX has one unit with no backup in case of equipment malfunction or other type of failure. (Some cautious oxygen users have actually reported purchasing more than one LOX unit in case one unit should fail.) With carbon composite cylinders, multiple cylinders provide continuous backup, and composite cylinders can also be used in conjunction with standard aluminum cylinders, allowing you to provide the most appropriate, cost-effective product mix depending on each user’s needs.
- Portable LOX systems are not allowed on airplanes for passenger use because of safety concerns. Composite cylinders can be used during air travel-in fact, because they are so easy to transport and handle, they are an ideal choice for all types of travel.
In short, Luxfer carbon composite medical cylinders offer the compact size, lightness of weight, portability and lifestyle enhancements offered by LOX systems-but without the significant financial and safety drawbacks.
Carbon composite cylinders for medical oxygen – what advantages do Luxfer carbon composite cylinders offer a homecare company?
Getting your company involved with composite cylinder technology in the early stages will give you the opportunity to differentiate your company from your competitors and take advantage of growing referrals from medical prescribers in your area. This new technology will set you apart as an innovative, future-oriented company, helping you not only to retain existing customers but also to attract new ones as Luxfer’s advertising and other promotional activities build awareness and preference for carbon composite cylinders.
Most of all, you will be providing the most advanced cylinder technology that will truly improve the quality of life for oxygen users you serve. Composite cylinders provide the following major clinical benefits for users:
- Significantly lighter weight improves ambulation and mobility and helps oxygen users lead more active lives, which physicians regard as therapeutically important.
- More oxygen per cylinder increases the duration of ambulation and enables oxygen users to exercise more and to participate more actively in longer-term activities with fewer cylinders.
- In short, because of their lighter weight, more compact size and longer-lasting oxygen supply, Luxfer composite cylinders give oxygen users greater freedom and help them get more out of life.
Because Luxfer carbon composite cylinders hold more oxygen in a much smaller package than comparable steel or aluminum cylinders, composite cylinders will significantly decrease your delivery costs by leaving more oxygen with the user with each trip-that means fewer visits and less transportation cost. Composite cylinders are about half the weight of comparably sized aluminum cylinders, but composites offer significantly more oxygen capacity because they can be filled to 3,000 psi. For example, an M09B composite cylinder is the same size package as an M6 aluminum cylinder, but the composite cylinder can hold 50% more oxygen.
Luxfer composite cylinders are a cost-effective, profitable alternative to expensive liquid-oxygen (LOX) systems. Composite cylinders offer all the clinical advantages of LOX without the significant financial and safety drawbacks. (See the next question for a more detailed discussion of this point.)
Luxfer composite cylinders also offer you an outstanding opportunity for retail sales. If you had family members who needed oxygen, wouldn’t you be willing to invest in the best equipment to improve the quality of their lives? Research has shown conclusively that many people pay more for products that enhance their lifestyle. This is particularly true of the aging “baby boom” population in the U.S, the largest and most affluent generation in American history-and also the most brand-conscious and technology-focused. This huge population segment begins turning 60 in 2006, and demographic experts are predicting that they will have a major impact on retail sales of medical devices of all types, including oxygen delivery systems. The “boomers” will demand the real advantages provided by Luxfer carbon composite cylinders.
Carbon composite cylinders for medical oxygen – why is Luxfer offering carbon composite cylinder technology for medical oxygen?
Carbon composite cylinder technology provides significant clinical benefits to patients, especially those who are ambulatory. Physicians often encourage ambulation for oxygen patients, and cylinder weight is an important factor in a patient’s ability to remain active. Luxfer carbon composite cylinders are the lightest-weight portable oxygen cylinders available in the market today, which makes them an ideal choice for ambulatory patients.
Luxfer composite cylinder technology has been widely used for home oxygen therapy in Japan for more than 15 years and in Europe for nearly a decade—and in both these demanding markets, use of composite cylinders continues to grow for medical oxygen, as well as other applications.
The U.S. is now emerging as the next major market for medical composite cylinder technology. More than a half-million Luxfer composite cylinders are already in use in the U.S. as part of self-contained breathing apparatus (SCBA) life-support systems for firefighters, and use of composites for emergency medical services (EMS) is on the rise. This proven Luxfer cylinder technology is ideal for home medical use as well, and Luxfer is now making it available for homecare providers and medical institutions.
Luxfer is the world’s largest manufacturer of aluminum and composite cylinders with four manufacturing facilities in the U.S., as well as plants in England, France and Australia.
Aluminum scuba cylinders in oxygen-enriched and oxygen service – do fires occur frequently with aluminum oxygen cylinders in general?
Absolutely not. Oxygen-related fires are extremely rare events, which is a testimony not only to the safety and suitability of aluminum cylinders for oxygen service, but also to proper cleanliness, care and maintenance. Aluminum cylinders have been used in oxygen service for more than 35 years, and more than 20 million cylinders have been produced for such service in North America alone. However, because oxygen-related fires happen infrequently, people can become lax about oxygen safety—which is the greatest danger of all.
Aluminum scuba cylinders in oxygen-enriched and oxygen service – I’ve heard about fires and explosions occurring in tanks that were supposedly cleaned for oxygen. How could that happen?
There are two main possibilities. First, the cylinder might well have been properly cleaned and tested, but subsequently became contaminated in a way that was not detected before the fire occurred. Sometimes other elements of the oxygen filling or containment system become contaminated, and they, in turn, contaminate the cylinder; sometimes a valve is improperly installed into the cylinder or an improper lubricant is used; sometimes contamination occurs during use—the possibilities are numerous. Or, second, the cylinder was not cleaned and tested properly in the first place, and a contaminant was still present to serve as fuel for the fire. One thing is certain: An oxygen-fed fire cannot start without oxygen, an ignition source and a contaminant—so contamination must have been present.
Aluminum scuba cylinders in oxygen-enriched and oxygen service – what happens to an aluminum scuba tank in an oxygen-fed fire?
- First, an ignition source of some sort—a flame or spark, excessive or prolonged heat, impact, etc.—ignites a contaminant, which serves as the initial fuel for the fire. Please remember: many materials that might not ignite and burn in standard air under normal atmospheric pressure will ignite and burn, often furiously, in a high-pressure, oxygen-rich environment.
- The initial fire begins melting the metal of the cylinder and/or the scuba valve, at which point the molten metal itself becomes fuel and starts to burn. The melt temperature for aluminum is 1,220 degrees F (660 degrees C), which gives you some idea of how hot an oxygen-fed fire can become—and it usually reaches these elevated temperatures in less than one second. All the time that the metal is burning, oxygen is being consumed and the fire is intensifying.
- The action of the fire rapidly increases the pressure inside the cylinder, and all the while more and more aluminum is melting and starting to burn, fueling the fire and weakening the cylinder to the point that it can no longer hold the growing pressure. All this occurs so quickly that the pressure-relief device on the valve does not have time to activate.
- By the time the pressure-relief device is ready to activate, either the valve is forcefully ejected at high velocity or the cylinder ruptures—or both.
- Afterwards, it is very difficult, if not impossible, to determine the nature of the original contaminant, because the contaminant has been completely consumed or driven off by the extremely hot fire. At that point, a thorough examination of the total oxygen system, cleanliness records, cleaning methods, system use, care and maintenance records, filling procedures and other relevant data may reveal possible sources of contamination.
Aluminum scuba cylinders in oxygen-enriched and oxygen service – can dropping or striking a scuba tank containing pressurized oxygen start a fire?
If a contaminant (fuel) is present and the oxygen inside a cylinder is under sufficient pressure, impact from a fall or blow can indeed be the ignition source for an oxygen-fed fire. Although ignition of this type occurs very rarely, it’s still a good idea to handle a pressurized cylinder with care at all times. Always follow all applicable DOT guidelines when transporting cylinders. Secure cylinders when transporting them so that they will not roll around, rattle about or strike other cargo or hard surfaces. Protect cylinders from falling and impact by using chain restraints, padding, straps and dollies during transportation and use. Also, always exercise great caution when hand-carrying all pressurized scuba cylinders, especially those containing oxygen or oxygen-enriched mixtures.
Carbon composite cylinders for medical oxygen – how often must carbon composite cylinders be retested?
Luxfer’s carbon composite cylinders must be retested (i.e., requalified for continued service) every five years, the same as aluminum oxygen cylinders. In fact, Luxfer was the first company to receive a full five-year requalification exemption for its carbon composite cylinders from the U.S. Department of Transportation. (Some competitive composite cylinders must be requalified every three years.)
Aluminum scuba cylinders in oxygen-enriched and oxygen service – it’s really important that I have enough pure oxygen in my decompression cylinder when I need to use it after a deep dive. Is it okay to put extra oxygen in my cylinder to make sure that I don’t run out?
DOT regulations (see CFR 49) strictly prohibit over-pressurizing a scuba cylinder containing any kind of gas, but it is particularly dangerous to do so with high oxygen concentrations. The reason is: The higher the pressure and the higher the oxygen concentration, the higher the risk of a fire and explosion if a contaminant is present.
Luxfer has received numerous and persistent reports that technicians in certain sectors of the recreational diving community routinely over-pressurize scuba cylinders, including cylinders containing high concentrations of oxygen. This is sometimes described as “doing divers a favor,” offering “a little more down time” or “giving divers their money’s worth.” Not only is this an unsafe practice, it is against the law! Under no circumstances should you allow the gas pressure in your scuba cylinder to exceed the service pressure for which the cylinder is designed and stamped or marked. If a filler offers to over-pressurize your cylinder, you should not only refuse the offer, you should report the filler to the DOT. If you suspect that your cylinder has been over-pressurized, you should have it depressurized and have it inspected by a competent technician to determine whether it is fit for further service.
For pure oxygen, DOT mandates strict pressure limits: Gas pressure in an aluminum cylinder containing pure oxygen must never exceed 3,000 psi (even if the cylinder is stamped for a pressure above 3,000 psi).
If you are concerned about running out of oxygen, use a larger decompression cylinder filled to the proper service pressure—or carry more cylinders.
Aluminum scuba cylinders in oxygen-enriched and oxygen service – I’d like to start using nitrox (EAN) in a scuba tank in which I’ve only been using air. Can I do that?
Yes, if you have the cylinder properly cleaned and tested for oxygen and oxygen-enriched service (i.e., oxygen concentrations above 23.5%).
Aluminum scuba cylinders in oxygen-enriched and oxygen service – are Luxfer scuba cylinders ready for oxygen service when they leave the Luxfer factory?
New Luxfer scuba cylinders manufactured from January 1, 2000, until December 31, 2004, were cleaned for oxygen service at the factory and sealed with an oxygen-compatible cap before being shipped. However, starting on January 1, 2005, Luxfer began providing oxygen-clean scuba cylinders only by special order. Unless specifically ordered “oxygen clean,” new Luxfer scuba cylinders will be cleaned for gas mixtures containing only up to 23.5% oxygen. (Of course, it will still be possible to have these cylinders cleaned for use with higher concentrations of oxygen by following the DOT-specified procedures cited above.)
Aluminum scuba cylinders in oxygen-enriched and oxygen service – how do I keep my cylinder clean for use with oxygen or oxygen-enriched gas mixtures?
Here are some basic guidelines for keeping your cylinder clean and for using it with oxygen and oxygen-enriched gas mixtures (more detailed guidelines are available from CGA):
- Only use an oxygen-clean, oxygen-compatible valve installed by a properly trained, competent technician familiar with the procedures described in current CGA guidelines.
- Either use no lubricants at all—or use only lubricants that the lubricant manufacturer explicitly recommends for use with oxygen systems and cylinders containing oxygen under pressure. Once you have found an oxygen-safe lubricant, always strictly follow the application and use instructions of the lubricant manufacturer. If a lubricant manufacturer does not specifically state that a lubricant is suitable for compressed oxygen service, don’t use it.
- Have your cylinder filled only with contaminant-free gas pumped by oxygen-clean systems, including fill lines that are clean and dedicated only to oxygen service and compressors that will not release oils or other contaminants into the gas.
- Make sure that the inside of your cylinder does not become contaminated by water, dirt, oil residues, body fluids or other contaminants during use and storage. If the cylinder does become contaminated, it must be re-cleaned and tested before being used with oxygen again.
- If a hydrocarbon or other contaminant is discovered on the outside of the valve-to-cylinder connection, the cylinder must be depressurized and tested to make sure that it is still oxygen-clean. If the cylinder is not clean, then it must be re-cleaned for oxygen and tested again before being filled with oxygen or an oxygen-enriched gas mixture.
- Ensure that your cylinder is inspected and requalified only by properly trained, competent technicians who are familiar with government requirements regarding oxygen cleanliness and use. If you suspect that your cylinder has been handled by someone who lacks this requisite knowledge, do not use the cylinder for oxygen or oxygen-enriched service until the cylinder has been tested by competent people.
- A valve should only be removed and reinstalled by a properly trained, competent technician who is familiar with procedures described in current CGA guidelines (see CGA P-38). Attempting to remove a valve without following the proper safety procedures can cause death or serious injury.
- If a cylinder owner, user, inspector, requalifier, distributor or filler has any doubts concerning the proper cleanliness of a cylinder intended for oxygen or oxygen-enriched service, the cylinder must be tested for oxygen cleanliness before being filled or used.
- When your cylinder has been exposed to possible contaminants, have it cleaned and tested for oxygen-cleanliness before filling or using it.
Aluminum scuba cylinders in oxygen-enriched and oxygen service – what is the difference between “formal” and “informal” oxygen cleaning?
The terms “formal oxygen cleaning” and “informal oxygen cleaning,” which appear in some non-Luxfer scuba manuals, are intended to differentiate between formal, government-mandated oxygen-cleanliness documentation required in the gas and medical industries, as opposed to less-formal documentation used in the recreational diving industry.
Unfortunately, some scuba technicians and divers have erroneously interpreted “informal cleaning” to mean that a less-rigorous, less-thorough level of oxygen cleaning is required for scuba equipment—even though the scuba manuals that use these terms make it quite clear that the same careful cleaning procedures and acceptable cleanliness levels should be used with all equipment in oxygen service. Moreover, the term “informal” is often associated with the so-called “40% rule,” from which some divers and technicians have wrongly inferred that the recreational diving industry somehow has special dispensation to clean cylinders to a less-stringent standard and at a higher oxygen-content threshold than other industries (see Question 4, above).
Because of these erroneous and potentially dangerous misinterpretations, Luxfer chooses not to use the terms “formal” and “informal” when referring to oxygen cleanliness. Oxygen clean is oxygen clean—there are not different levels of cleanliness.
As for documentation, it is always a good idea to thoroughly document all aspects of your oxygen-cleaning procedures and maintenance. Such careful record-keeping can be very valuable if an oxygen-related incident occurs.
Aluminum scuba cylinders in oxygen-enriched and oxygen service – how clean does my cylinder actually need to be for oxygen service?
It needs to be “oxygen clean”—which means free from contaminants that can be the fuel for an oxygen-fed fire. Cleanliness on surfaces is measured by milligrams (mg) of hydrocarbon per square foot of surface area (mg/ft2). In the U.S., DOT (in RRC 901c) requires that the cleanliness of cylinders used in oxygen service be proven to be less than 2.5 mg/ft2, which is a level considerably below what can be seen by the naked eye. For this reason, a visual inspection after cleaning is not enough. A test must be performed to verify that the required cleanliness level has been achieved. In CFR49 173.302(b), DOT specifies an approved cleaning method and a standard test to determine the cleanliness of cylinders.
Aluminum scuba cylinders in oxygen-enriched and oxygen service – why does Luxfer require cleaning for oxygen concentrations above 23.5%?
Few concepts have caused more confusion and controversy in the recreational diving industry than the so-called “40% rule.” While there seems to be general agreement that special cleaning is required when a pressurized oxygen concentration reaches a particular “threshold” percentage, there is disagreement about exactly what that threshold should be and at what pressure it becomes important. Some say 40%; others say 23.5%; still others say anything more than 21% when a gas mixture is pressurized more than 100 psig. It would be helpful to explore the background of this confusion briefly before discussing Luxfer’s position on this vital subject.
The 40% threshold is cited in a single Federal CFR published by the Occupational Safety and Health Administration (OSHA) of the U.S. Department of Labor: 29CFR910.430, which applies to “Commercial Diving Operations” and states in the section titled “Oxygen safety” on page 854: “(1) Equipment used with oxygen or mixtures containing over forty percent (40%) by volume oxygen shall be designed for oxygen service. (2) Components (except umbilicals) exposed to oxygen or mixtures containing over forty percent (40%) by volume oxygen shall be cleaned of flammable materials before use.”
Please note that OSHA also provides a very specific definition about who should—and should not—be considered a “commercial diver” to whom the 40% threshold applies: “Commercial diver means a diver engaged in underwater work for hire excluding sport and recreational diving and the instruction thereof” (46CFR197, page 409; italics added for emphasis).
Even though OSHA clearly excludes sport and recreational divers from the CFR that specifies a 40% threshold, some professionals in the recreational diving industry have nonetheless been citing the OSHA “rule” for many years and maintaining that special cleaning of recreational diving equipment is not necessary with oxygen concentrations of 40% or less. These advocates of the “40% rule” have often stated that the U.S. Navy supports their position, which at one time was true—but no more. In the current applicable military specification (Mil-Std-1330D), the Navy specifies a 25% threshold for oxygen cleaning. Compounding the confusion is the fact that two other OSHA documents, 29CFR1910.146 and 29CFR1910.134, specify an oxygen threshold of 23.5%.
For the sake of clarity, here’s a summary of the oxygen threshold percentages at which various key U.S. agencies and organizations require special cleaning of oxygen-handling equipment and systems:
Organization Oxygen threshold ReferenceU.S. Navy
>25%
Mil-Std-1330D
U.S. Compressed Gas Association (CGA)
>23.5%
CGA Pamphlet 4.4
National Fire Prevention Association (NFPA)
>21 – 25%
NFPA standards
American Society for Testing & Materials (ASTM)
>25%
G126, G128, G63, G94
National Aeronautical & Space Administration (NASA)
>21%/>100 psig
Various KSC & JSC
Occupational Safety & Health Administration (OSHA)
>23.5%
29CFR1910.146
OSHA
>23.5%
29CFR1910.134
OSHA
>40%
29CFR1910.430
The reasons for Luxfer’s position: Luxfer supports an oxygen-cleaning threshold of 23.5% and does not support the alleged “40% rule.” This means that when a pressurized oxygen concentration used in a Luxfer cylinder exceeds 23.5%, the cylinder must have been cleaned to the same cleanliness standard mandated for a cylinder containing 100% oxygen. Luxfer’s reasons for this position are:
- All key U.S. regulatory and gas industry references except one advocate an oxygen threshold of 21% to 25%.
- Luxfer is a member of the Compressed Gas Association and therefore supports the CGA-specified threshold of 23.5%. Furthermore, Luxfer defers to CGA on all safety matters related to oxygen handling and containment, as do OSHA and DOT.
- As an international manufacturer, Luxfer works with regulatory authorities and industry associations around the world—the overwhelming majority of which support a threshold value from 21% to 25% (for example, this is true in the United Kingdom, Australia, France, Germany and Japan).
- United Nations compressed air packaging guidelines (see UN 1002) indicate that when compressed air contains oxygen as the only oxidizing gas and the oxygen concentration exceeds 23.5%, then the entire gas mixture must be listed as an oxidizing gas.
Some within the recreational diving community contend that the supposed “40% rule” is justified by an excellent scuba safety record and should therefore be maintained—despite the fact that so many agencies and organizations have specified much lower threshold values for oxygen cleaning. Luxfer finds this “history-of-use” argument unconvincing for the following reasons:
- Compared to other industries and organizations that use pressurized oxygen, oxygen usage in the recreational diving industry has not been sufficiently widespread, nor are available oxygen-use statistics sufficiently comprehensive, to declare a successful history of use for the 40% threshold.
- Oxygen-related fires and explosions are inherently low-probability, high-consequence events—which means that they occur very infrequently, but are usually catastrophic when they do. Forensic evidence has shown that undetected, non-propagating fires happen within scuba oxygen systems more frequently than is generally known. It is possible to operate “on the edge” of a fire for years without knowing it—and to be lulled into complacency by seemingly “safe” performance.
- As use of higher oxygen concentrations at higher pressures increases in the recreational diving industry, the risk of serious accidents will also increase.
Under these circumstances, Luxfer believes that requiring thorough oxygen cleanliness at a threshold of 23.5% makes very good sense not only for the sake of individual safety, but also from the business standpoint of prudent risk management.
Aluminum scuba cylinders in oxygen-enriched and oxygen service – why is it necessary to clean scuba tanks for oxygen service?
To remove contaminants that can become the fuel for an oxygen-fed fire.
Oxygen, an oxidizing gas, does not burn, but it supports combustion and causes other materials to burn. In the presence of pressurized oxygen concentrations exceeding that in standard air, most materials become progressively more flammable and ignitable as the oxygen concentration and pressure increase. Even materials that would not easily catch fire in standard air under normal atmospheric pressure will ignite and burn furiously in a pressurized oxygen-enriched environment. It cannot be overemphasized that rising pressure increases the risk of ignition.
For an oxygen-fed fire to occur, three things must be present: oxygen, fuel (something to burn), and heat (an ignition source)—this is the classic “fire triangle.” When dealing with pressurized oxygen or EAN in a scuba cylinder, remember this important variation on the classic three factors needed for a fire:
- Oxygen or gas containing oxygen, under pressure (higher concentrations of oxygen and significant pressure greatly increase the need for oxygen cleanliness and diligent safety practices).
- An ignition (flame, spark, heat source, etc., including impact from dropping or striking a pressurized cylinder).
- A contaminant (i.e., fuel—but the reason the term “contaminant” is preferred in this case is that in an properly cleaned oxygen system, no fuel is present. If fuel is present, it is contaminating the system and making it no longer safe for use with oxygen). Common contaminants include:
- Machining oils (including residual oil film)
- Hydrocarbon-based grease and lubricants (including compressor oil)
- Some soaps, detergents, solvents and cleaning solutions, especially those that contain organic compounds
- Skin lotions and emollients and cosmetics
- Sun-tanning oils and lotions
- Human skin oil and bodily fluids
- Insects and insect body parts
- Paint, wax, and marking crayons
- Carbon dust from filtration systems
- Metal fines, filings, scale and burrs
- Chrome chips (usually from valves and other chrome-plated parts)
- Rust particles and dust
- Metallic oxides in general
- Airborne soot and dust
- Pipe thread sealants
- Residue from soapy water and leak-detection fluids used to check for leaks
- Lint from cloths used in cleaning
- Any other material containing organic compounds and hydrocarbons
Any of these contaminants—many of which are very difficult to detect—can be the initial fuel for an ignition event, the technical term for starting a fire. Once an oxygen-fed fire gets going, even metal components—including a scuba cylinder itself—can burn vigorously. Aluminum melts at 1,220 degrees F (660 degrees C); after an oxygen-related cylinder fire, it is not unusual to find large areas of melted aluminum—which shows just how hot and energetic such a fire can be.
That’s why it’s so essential to remove contaminants and to keep the oxygen system clean. Proper oxygen cleaning need not be excessively costly or time-consuming, but it does need to be effective. Removing contaminants and keeping equipment oxygen-clean is the best way to make sure that an oxygen-fed fire never starts.
A number of agencies and organizations in the United States provide certification courses in oxygen cleaning. For example, American Nitrox Divers International (ANDI) offers a particularly comprehensive training course that defines “oxygen cleaning” as “the process of contaminant removal from component parts or assemblies intended for contact with gases containing Oxygen concentrations of 23.5% or more by volume.”1
1EAN and Oxygen Equipment Servicing Procedures, ANDI International: 1999, p. 19.
Aluminum scuba cylinders in oxygen-enriched and oxygen service – can I fill my Luxfer aluminum scuba cylinder with pure oxygen so that I can use it for decompression?
Yes, if you follow the Luxfer requirements listed below, which must be met both for pure oxygen and gas mixtures containing more than 23.5% oxygen:
- The cylinder must have been properly cleaned, tested for cleanliness and maintained in a proper state of cleanliness for oxygen service in strict accordance with the Code of Federal Regulations (CFR), specifically U.S. Department of Transportation (DOT) CFR49 173.302(b).
- The cylinder must be equipped with an oxygen-compatible valve and be filled only by oxygen-clean, properly maintained filling equipment dedicated to oxygen service.
- The cylinder must never be fast-filled or over-pressurized.
- Proper safety procedures for handling and dispensing oxygen prescribed by the DOT and U.S. Compressed Gas Association (CGA) must be followed at all times. In fact, Luxfer further recommends that anyone in the scuba industry who handles pure oxygen in a Luxfer cylinder become familiar with and follow current guidelines concerning cleanliness, filling, storage, usage and maintenance of oxygen cylinders provided by the U.S. Food and Drug Administration (FDA). As the world’s largest manufacturer of aluminum and composite medical oxygen cylinders, Luxfer has a great deal of experience with cylinders in pure oxygen service and with the FDA guidelines that promote safe oxygen usage. Luxfer’s experience has shown that following FDA guidelines is a practical and effective way of preventing oxygen-related accidents.
Sustained-load cracking – if Luxfer 6061-alloy cylinders are not susceptible to SLC, why has Luxfer exchanged 6061 cylinders that have been reported to have cracks?
- After the introduction of eddy-current technology, Luxfer received reports of cracking in 6061-alloy cylinders. We accepted returns on about 1,200 of these cylinders to conduct extensive tests. Not a single cylinder was found to be cracked.
- On Luxfer 6061-alloy cylinders, eddy-current devices sometimes show harmless “indications” that lead to “false-positive” readings for SLC.
Should I be doing anything different for my aluminum alloy 6061 composite cylinders than I have done in the past?
If you have properly maintained, used, tested and stored your cylinders in accordance with applicable regulations and manufacturer recommendations, the answer is no. If you continue following these proper procedures, your cylinders should provide many years of dependable service.
For more information about proper care and maintenance for your aluminum and aluminum-lined composite cylinders, please see the “Support” section of the Luxfer website at www.luxfercylinders.com.
Are special coatings needed to protect aluminum cylinder interiors from tap water?
No. Special internal cylinder coatings are sometimes used with certain kinds of gases, but they have nothing to do with protecting a cylinder from tap water or any other kind of water, nor are they required or recommended for that purpose.
Will my aluminum-lined composite cylinder have a shortened life from being hydrostatically tested with tap water?
No. The field record of cylinders in use for many years shows no evidence of reduced service life from periodic hydrostatic testing with tap water. This test is normally conducted quickly, and the cylinder only holds tap water for a few minutes. After the test, the cylinder must be dried. As long as this procedure is properly followed, there is no cause for concern.
Does hydrostatically testing an aluminum-lined composite cylinder with tap water corrode the cylinder or make the cylinder unsafe?
No. Tap water of varying quality from all around the world has been used to hydrostatically test and retest aluminum and aluminum-lined composite cylinders for more than 30 years without harming cylinders or making them unsafe to use—provided, of course, that the cylinders have been properly dried after testing, as required by regulation. The worldwide safety record for some three million aluminum-lined composite cylinders is excellent, which affirms that tap water is an appropriate hydrostatic test liquid. Moreover, test agencies have an excellent record of properly drying cylinders before releasing them for service. In short, based on Luxfer field experience and user feedback, tap water corrosion of aluminum and aluminum-lined composite cylinders in the field is not a problem.
Should I avoid leaving tap water inside aluminum cylinders made from alloy 6061?
Yes. Do not leave tap water or any other kind of water inside any aluminum or aluminum-lined cylinder—or any steel cylinder, for that matter. Water remaining inside a cylinder is considered a “contaminant.” Luxfer, as well as regulatory authorities around the world, have required for years that cylinders be kept free of contaminants. If a cylinder becomes contaminated with tap water, pure water, sea water, oil, grease or other contaminating substances, the cylinder should be removed from service, properly cleaned, thoroughly dried and diligently inspected before further use. However, in some countries, regulations or standards require that cylinders containing water be condemned and rendered unserviceable (for example, see ISO 10461, Section 14.2). In short, if you find water or other contaminants inside your cylinder, take it out of service and comply with all applicable regulations.
As far as 6061 aluminum alloy is concerned, cylinders made from this alloy have been used for decades in scuba and shipboard service, in which cylinders are periodically exposed to very corrosive salt water and brine. These cylinders have an outstanding record both for service and safety. However, at no time should cylinders be stored sitting or standing in water—they should be stored in a clean, dry place—and water should never be allowed to remain inside cylinders. The only time that cylinders should contain water is during the very brief period required to perform a hydrostatic test (see questions 2 and 3, below), and the cylinders should be immediately dried when the test is completed.
Sustained-load cracking – should I stop using my 6351-alloy scuba tank?
No. As long as your 6351-alloy scuba tank is properly inspected and requalified in accordance with regulations in Australia and New Zealand, there is no reason why you cannot continue to use it.
Sustained-load cracking. I’ve heard that Luxfer have closed their plant in Australia and that they are no longer manufacturing scuba tanks. Is that true?
No. Luxfer has not stopped manufacturing scuba tanks. The Luxfer plant in Australia was closed in 2004 during a consolidation of Luxfer’s global manufacturing capacity. However, Luxfer has maintained a sales office and distribution center near Sydney. The Luxfer tanks now sold in Australia are manufactured at the Luxfer plant in California, which produces more aluminium tanks than any other facility in the world. Luxfer also manufactures scuba tanks in England. Luxfer remains fully committed to supplying the highest-quality tanks to the scuba industry worldwide.
Sustained-load-cracking – I’ve seen evidence on the Internet that a Luxfer scuba tank exploded in Perth, Australia, early in 2005. Was SLC involved?
An older scuba tank did, in fact, rupture in Perth in January 2005, and the likely mode of rupture was SLC. The investigation is ongoing. However, the 6351-alloy tank involved in the accident was not manufactured by Luxfer, but by CIG Gas Cylinders, a company acquired by Luxfer in 1997. CIG Gas Cylinders used 6351 alloy to manufacture scuba tanks from 1975 through 1990, and then switched to 6061 alloy. All scuba tanks manufactured in Australia by Luxfer have been made from Luxfer’s proprietary 6061 aluminium alloy, which is not susceptible to SLC.
Sustained-load cracking – how often should my Luxfer 6351-alloy scuba tank be inspected?
- DOT requires requalification (hydrostatic retesting and visual inspection) of all aluminum scuba tanks every five years, regardless of alloy.
- Both the DOT and the U.S. scuba industry recommend an annual visual inspection for all 6351-alloy scuba tanks. Luxfer supports this recommendation.
- For its 6351-alloy tanks, Luxfer has established a manufacturer’s requirement for a visual inspection, including an eddy-current test, at least every 2.5 years.
Differences among the terms oxygen service – oxygen mixture – nitrox – enriched-air nitrox EAN – oxygen-enriched air
The term oxygen service generally means using pure oxygen (oxygen concentrations of 95% to 100%), but the term is sometimes used more broadly to refer to any gas mixture containing more oxygen than air. The “standard air” we breathe is composed of 20.95% oxygen, 78.05% nitrogen and 1% of trace amounts of other gases, including argon, carbon dioxide, neon, helium, krypton and xenon (the amounts vary depending upon your geographical location, altitude, etc.). For practical purposes, most technical literature rounds off these percentages and defines “standard air” as 21% oxygen and 79% nitrogen.
Oxygen mixture generally refers to gas blends containing between 50% and 95% oxygen.
Oxygen – enriched air, nitrox , and enriched-air nitrox (EAN) are generally used synonymously in the diving industry since all refer to pressurized diving gas mixtures containing various oxygen concentrations greater than standard air. For example, two common mixtures used by divers are EAN 32 (32% oxygen) and EAN 36 (36% oxygen). However, in the gas industry, oxygen-enriched air is sometimes defined more specifically as gas mixtures containing more oxygen than found in standard air, but no more than 50% oxygen.
To avoid confusion, Luxfer prefers using the term oxygen service to refer only to pure oxygen usage and enriched-air nitrox (EAN) to refer to oxygen-enriched breathing mixtures used for diving.
Whatever term you choose, the main thing to remember concerning Luxfer scuba cylinders is that when you fill a cylinder with an oxygen concentration of 23.5% or more, that cylinder must be specially cleaned for oxygen service as though it contained 100% oxygen.
Sustained-load cracking – how can I tell if my Luxfer cylinder is made from 6351 alloy?
The easiest way is to check the original hydrostatic test date stamped on the cylinder crown. Luxfer manufactured 6351-alloy cylinders during the following periods:
- United States: 1972 through mid-1988
- England: 1958 through 1995
After the above dates, Luxfer began making cylinders from a proprietary 6061 alloy, which is not susceptible to SLC.
In Australia, CIG Gas Cylinders manufactured scuba tanks from 6351 alloy from 1975 through 1990, and then switched to 6061 alloy. Luxfer acquired CIG Gas Cylinders in 1997, by which time Luxfer was manufacturing all scuba tanks with its own proprietary version of 6061 alloy. All Luxfer tanks manufactured in Australia under the names “Luxfer” and “Luxfer Australia ” have been made exclusively with Luxfer’s 6061 alloy.
Sustained-load cracking – how do I know if the person inspecting my cylinders is properly trained?
- Luxfer recommends taking your cylinder to an authorized Luxfer service center or to an inspector trained by Professional Scuba Inspectors, Inc. (PSI) or the Association of Scuba Service Engineers & Technicians (ASSET).
- It cannot be overemphasized that the quality of inspection is far more important than the frequency of inspection! An untrained or improperly trained inspector can look at a 6351-alloy cylinder numerous times without detecting SLC.
- Unfortunately, many untrained or improperly trained technicians continue to inspect cylinders, and no uniform standards for inspector training and certification exist among regulatory authorities around the world.
- Luxfer is working with industry groups and government agencies to help establish such standards.
Sustained-load cracking – why is it necessary to have my 6351-alloy cylinder inspected with an eddy-current device?
- When properly used, eddy-current devices contribute significantly to early detection of hard-to-see sustained-load cracks. However, an eddy-current test is not a replacement for a diligent visual inspection by a properly trained inspector.
- Eddy-current devices are tools to enhance proper visual inspections.
- Eddy-current devices currently approved by Luxfer for use with Luxfer 6351-alloy cylinders are Visual Plus, Visual Plus II, Visual Plus III, and Visual Eddy. However, the only eddy-current device approved by Luxfer for use with cylinders made from Luxfer’s proprietary 6061 alloy is Visual Plus III.
Sustained-load cracking – if there have been so few SLC-related cylinder ruptures, why is there so much alarming information about them on the Internet?
A great deal of misinformation and exaggeration about SLC is attributable to rumors and inaccurate reports spread by word-of-mouth and the trade press, but especially by the Internet, where the proliferation of inaccuracies is widespread and essentially unregulated.
Sustained-load cracking – which types of cylinders are most susceptible to SLC-related ruptures?
- Any type of cylinder manufactured from 6351 alloy could conceivably develop a sustained-load crack over time if subjected to certain conditions.
- However, a cylinder is more likely to rupture in applications where pressure is higher and where overfilling and abuse occur more often.
- Historically, the applications most susceptible to SLC-related rupture are scuba and SCBA (life support).
Sustained-load cracking – how many aluminum cylinders have exhibited SLC?
- Out of a total population of approximately 1,073,000 Luxfer scuba cylinders made of 6351 alloy, only 1.25% have exhibited SLC.
- Out of Luxfer’s total 6.1-million population of 6351-alloy cylinders, the SLC rate is slightly less than 0.37%.
- While we do not have complete statistics on cylinders manufactured by other companies, industry experts estimate that out of a worldwide population of more than 30 million 6351-alloy cylinders, far less than 1% have exhibited SLC.
Sustained-load cracking – how quickly do the cracks grow?
- Very slowly, as extensive research by Luxfer and outside laboratories has shown.
- No scientific evidence supports rumors and claims of “fast crack growth.”
- Cracks typically take eight or more years to grow large enough to cause a cylinder leak.
- Because SLC growth is so slow, properly trained inspectors have adequate opportunity to detect cracks during the normal requalification process.
Sustained-load cracking – what is sustained-load cracking?
- SLC is a metallurgical phenomenon that occasionally develops in cylinders made of 6351 aluminum alloy, as well as in other types of pressure vessels and structural components under stress for sustained periods of time.
- SLC has occurred in cylinders manufactured by various companies, including Luxfer.
- Cylinders that have been mechanically damaged, over-filled or abused are more susceptible to SLC.
- SLC is not a manufacturing defect; it is a phenomenon inherent in the metal itself.
Carbon composite cylinders for medical oxygen – How long does a carbon composite cylinder last?
All composite cylinders have a 15-year service life in accordance with regulations around the world. In the United States, the service life is set by the U.S. Department of Transportation.
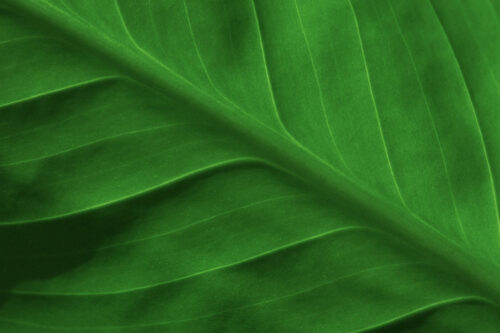
Support contact
Need assistance? Our global support team is here to help! Please complete the form below and we will reach out within 24-48 hours.