US +1800 764 0366 | Europe & Middle East +44 (0)115 980 3800 | Asia-Pacific: +61 2 7227 5369
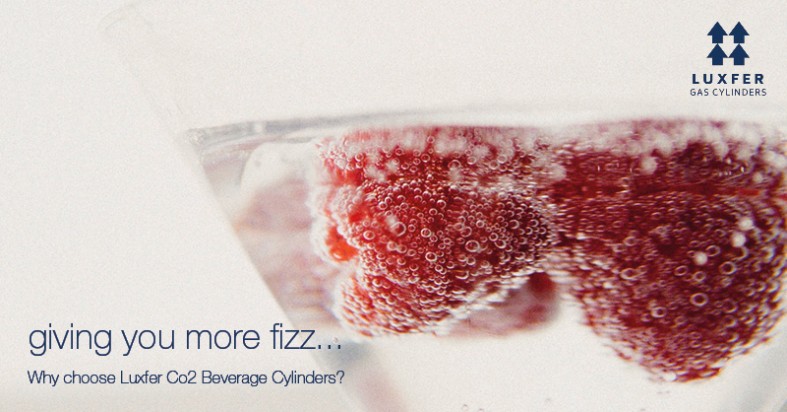
The beverage market has been hit by rising at-home consumption trends, impacted by COVID-19 lockdowns and the widespread shutdown of the hospitality sector across the UK.
Indeed, a February 2022 study of over 300,000 adults found that shop-bought alcohol consumption increased following the March 2020 lockdown and remained persistently higher than previous years throughout the rest of 2020, even when restrictions were lifted.
While the future is unpredictable, beverage brands could benefit from understanding how crucial cylinder technology is when it comes to remaining competitive in this crowded marketplace.
How gas is stored for the dispense of beverages such as soft drinks, lagers, ciders, stouts and bitters, isn’t just about safeguarding the fizz and the propulsion from the keg, it has a significant impact on taste and mouth-feel too, impacting customer satisfaction and brand loyalty.
The role of gas cylinders in drinks dispensing
The role of cylinders is to safely contain the gas in a sterile environment.
While CO2 is primarily used for soft drinks and lagers, various gas mixtures are involved in the dispense of ciders, stouts and bitters. Maintaining these – classified ‘food gases’ – at the correct pressure, preserves the stability in the keg.
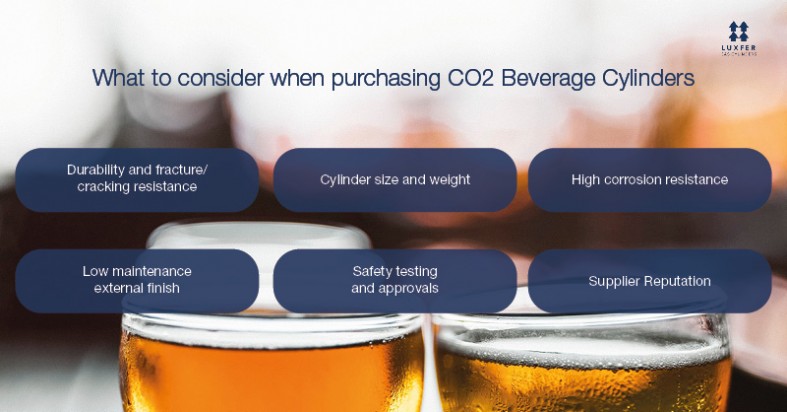
A range of factors are at play when it comes to choosing cylinders for this purpose:
Durability
The cylinder itself is a vital part of the gas dispensing system, meaning a high-quality cylinder with good resistance to fracture or cracking is paramount. As licensees and retailers grapple with rising costs,, poor cylinder quality poses a personal safety risk, and could potentially lead to writing off a large volume of stock.
Thanks to Luxfer’s metallurgic innovation, its beverage cylinder range is manufactured using a high-performance L6X® alloy. This proprietary formula has been specially optimised to deliver superior durability, fracture toughness and resistance to tearing and cracking.
Resistance to corrosion
Corrosion within the interior walls of a cylinder can occur with a poor quality product. This could affect the quality and taste of the drink and may also cause damage to the valves.
Currently more than 40 million L6X cylinders are in service around the world, demonstrating Luxfer’s exemplary record for safety and dependability.
Cylinder size and weight
The size and weight of a cylinder is key to safe handling, given that kegs are changed frequently by staff at pubs, restaurants, clubs, events and other food and beverage establishments.
Thanks to using an aluminium alloy, Luxfer’s cylinders for CO2 systems are among the most lightweight available, ranging from just 2kg to 25.5kg.
While the environment in which the cylinders dwell will differ by location, space is often at a premium in food and beverage outlets. Therefore, Luxfer offers a variety of cylinder sizes too, starting from 266mm in length, to 1,170mm.
Low maintenance
Beverage cylinders are routinely kept out of sight, beneath counters, in storage units and cellars. This means a low maintenance external finish is favourable because it limits the requirement to clean, re-paint or invest further attention by the staff, venue, brewery or retailer. Once installed, the cylinder performs with minimal add-on time or cost.
External finishes available from Luxfer to deliver this low maintenance product includes painting (wet paint and powder coating), mill finish (as-is after production), and brushed (where the exterior surface is brushed to make it smooth and remove any blemishes).
Reputation
Selecting a trusted supplier is important, with the BCGA raising awareness of outlets being targeted by non-reputable companies.
With 125 years of experience in gas containment, Luxfer has a proven track record providing solutions for this market. In fact, beverage CO2 cylinders were the first type of cylinders made by Luxfer in the UK in the 1950s – and the company was the very first to manufacture cold-extruded aluminium CO2 beverage cylinders.
Millions of beverage cylinders are in operation around the globe, with the US the largest customer base for Luxfer.
Safety testing
Adequate testing is fundamental to all cylinders and Luxfer is proud of its unrivalled safety record, which ensures quality and durability of its entire range and helps cement its enviable reputation.
This is manifested through stringent quality control checks. A hydrostatic test, where water is put into the cylinder at increasing pressure, is one of our mandatory testing procedures to ensure the product meets the required tolerances.
Luxfer also offers an active, global ‘Safety First’ programme to help its beverage customers use, maintain, and inspect high-pressure cylinders properly. This gives guidance on how best to handle and store CO2 cylinders, reinsert a valve and clean them. It not only promotes safety, it helps lower liability exposure.
And while CO2 cylinders currently occupy just five per cent of the company’s worldwide business, a controlled manufacturing process focusing on every operational detail – which Luxfer has perfected over many years and across many applications – produces a high-performance cylinder that is fit for purpose.
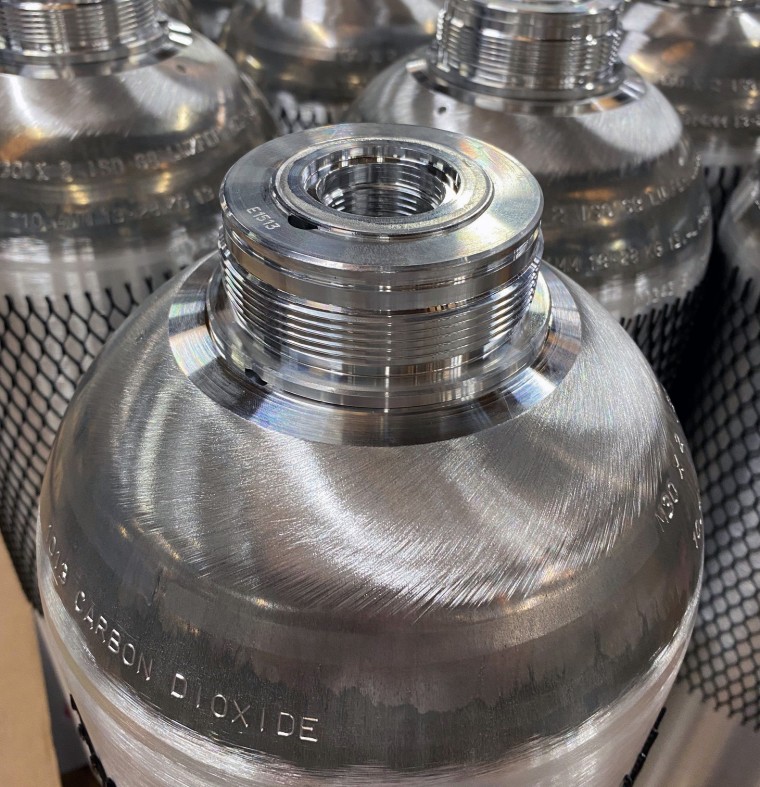
For more details on Luxfer’s beverage solutions, visit www.luxfercylinders.com/products/co2-cylinders/beverage